A stud welder is a body repair equipment. It is designed to straighten dents and repair damaged vehicle panels. Studs or pins are welded onto the damaged surface. Then, you simply pull the panels outward to reshape them.
This tool is essential for performing precise repairs without having to disassemble body panels.
The term “Tire clous” translates to “Stud welder” or “Stud puller” in American English.
SPOT WELDING / STUD WELDER
SOUDURE PAR POINT / TIRE CLOU
PUNKTSCHWEIBER / DENT PULLER
SOLDADOR POR PUNTOS / SOLDADOR DE PERNOS
SALDATURA A PUNTI / SALDATORE DI TASSELLI
Trusted and verified affiliates links
Introduction to the Stud welder
Definition and Operation
Definition:
A stud welder is a tool primarily used in body shops to straighten dents and deformations of metal panels. It works by welding studs or special pins onto the damaged surface of the metal panel. Once welded, these studs serve as anchor points to apply traction and straighten the panel.
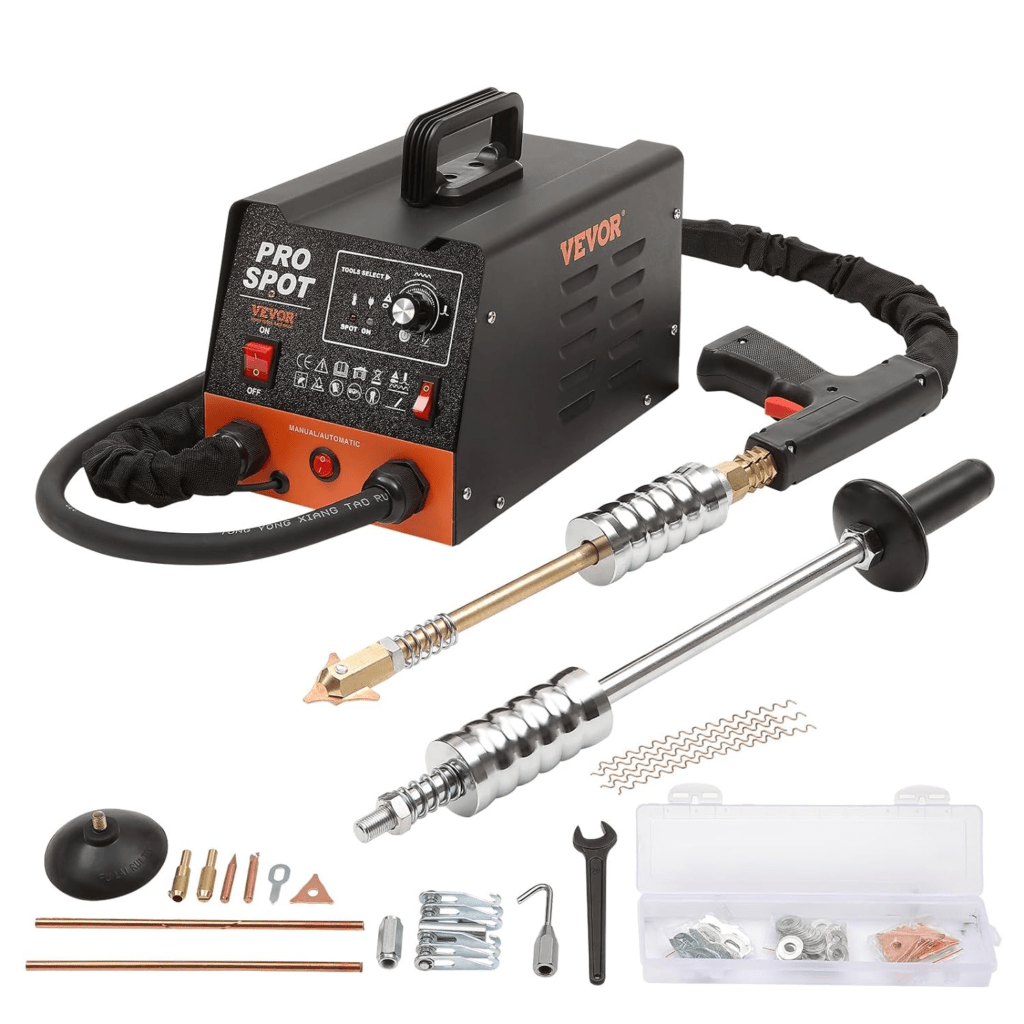
Operation:
Surface Preparation: The damaged area of the metal panel is cleaned to ensure good adhesion of the studs.
Welding the Studs: The stud puller quickly welds studs to specific points on the panel. The welding is done by a short burst of electric current through the stud, generating enough heat to fuse the metal of the stud with the panel.
Traction Application:
A traction tool (usually an inertia hammer or a lifting device) is attached to the welded studs. By pulling on this tool, the technician applies controlled force to straighten the panel.
Removing the Studs:
Once the panel is straightened, the studs are removed, and the surface can be sanded and finished to eliminate any remaining imperfections.
This process allows for the repair of body panels without having to disassemble parts, providing a quick, precise, and cost-effective solution for repairing damaged vehicles.
Importance of the Stud welder in the Bodywork Industry and Other Sectors.
The stud puller plays a crucial role in the automotive bodywork industry for several essential reasons:
Efficiency and Speed:
The stud puller allows for the quick and efficient straightening of dents and deformations in metal panels. Unlike traditional methods, which may require disassembling body parts, the stud puller enables on-site repairs, significantly reducing labor time.
Precision:
Thanks to the precise welding of studs at specific points, technicians can apply controlled traction exactly where needed. This precision ensures that the panel is straightened without creating new damage, which is essential for maintaining the integrity and appearance of the vehicle.
Repair Quality:
Repairs made with a stud puller are durable and of high quality. The fusion of the studs with the panel ensures a strong bond. It allows for the straightening of damaged areas with a smooth finish. This not only improves the aesthetic appearance but also the residual value of the vehicle.
Cost Reduction:
By eliminating the need to disassemble and reassemble vehicle parts, the stud puller reduces labor and material costs. Less disassembly also means less risk of secondary damage and associated additional costs.
Versatility:
The stud puller can be used on various types of metal, whether it is traditional steel or more modern materials like aluminum. This versatility is essential for adapting to different vehicle models and brands on the market.
Safety:
By enabling quick and precise repairs, the stud puller helps improve vehicle safety. A properly straightened body maintains the structural integrity of the vehicle, which is essential for occupant safety in case of a collision.
Reduced Environmental Impact:
By avoiding the complete replacement of metal panels, the stud puller helps reduce metal waste. This makes it a more environmentally friendly option compared to traditional repair methods.
The stud puller is an indispensable tool for professionals in the automotive bodywork industry. It combines efficiency, precision, and cost reduction while ensuring high-quality repairs. It is a technology that meets the modern demands of the automotive industry, offering quick and reliable solutions for vehicle repairs.
By integrating the stud puller into repair operations, body shops can not only improve the quality and efficiency of their repairs but also create a safer and more economical work environment. It is a wise investment that offers long-term benefits for both bodywork professionals and their customers.
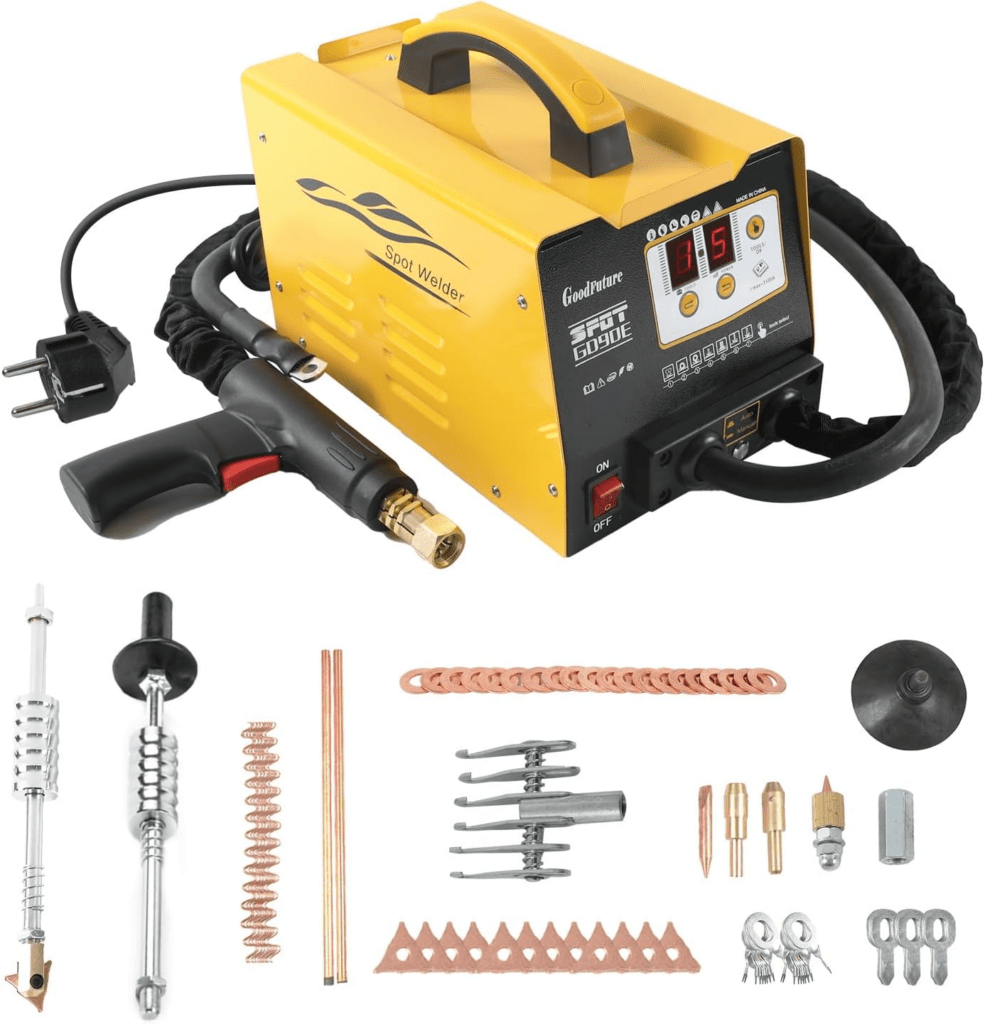
Description of Main Components (studs, pins, traction tool, etc.):
The stud puller is an essential tool in automotive bodywork for straightening damaged metal panels.
Here is a detailed description of its main components and their roles:
Welding Electrode:
Role: The electrode is the part of the stud puller that comes into direct contact with the stud or pin to be welded onto the metal panel. It conducts intense electric current that generates the necessary heat to fuse the stud with the metal surface.
Description: Generally made of copper or copper alloy for its high electrical conductivity and heat resistance, the electrode is designed to withstand repetitive welding conditions.
Welding Studs/Pins:
Role: The studs or pins are the anchor points welded to the damaged metal panel. They serve as traction points to straighten dents and deformations.
Description: They are made of steel or a material compatible with the panel to be repaired, available in various sizes and shapes to accommodate different types of damage and metals.
Traction Tool (Inertia Hammer, Extractor):
Role: This tool attaches to the welded studs and applies traction force to straighten the panel. The inertia hammer, in particular, allows pulling the panel outward with controlled, repeated strikes.
Description: The inertia hammer includes a movable weight on a rod, which slides and strikes against a stop to generate traction force. Extractors can also be manual or hydraulic for more controlled traction.
Welding Gun:
Role: The gun houses the electrode and allows the technician to precisely position the studs on the panel. It is designed to be ergonomic, facilitating prolonged use.
Description: Lightweight and maneuverable, it often features intuitive controls to regulate welding current and application duration.
Control Unit:
Role: This unit regulates the electric current sent to the electrode, ensuring precise and controlled welding. It allows for adjusting welding parameters based on specific repair needs.
Description: Equipped with settings for power, welding time, and sometimes even pressure, the control unit is the heart of the operation, guaranteeing consistent and quality welding.
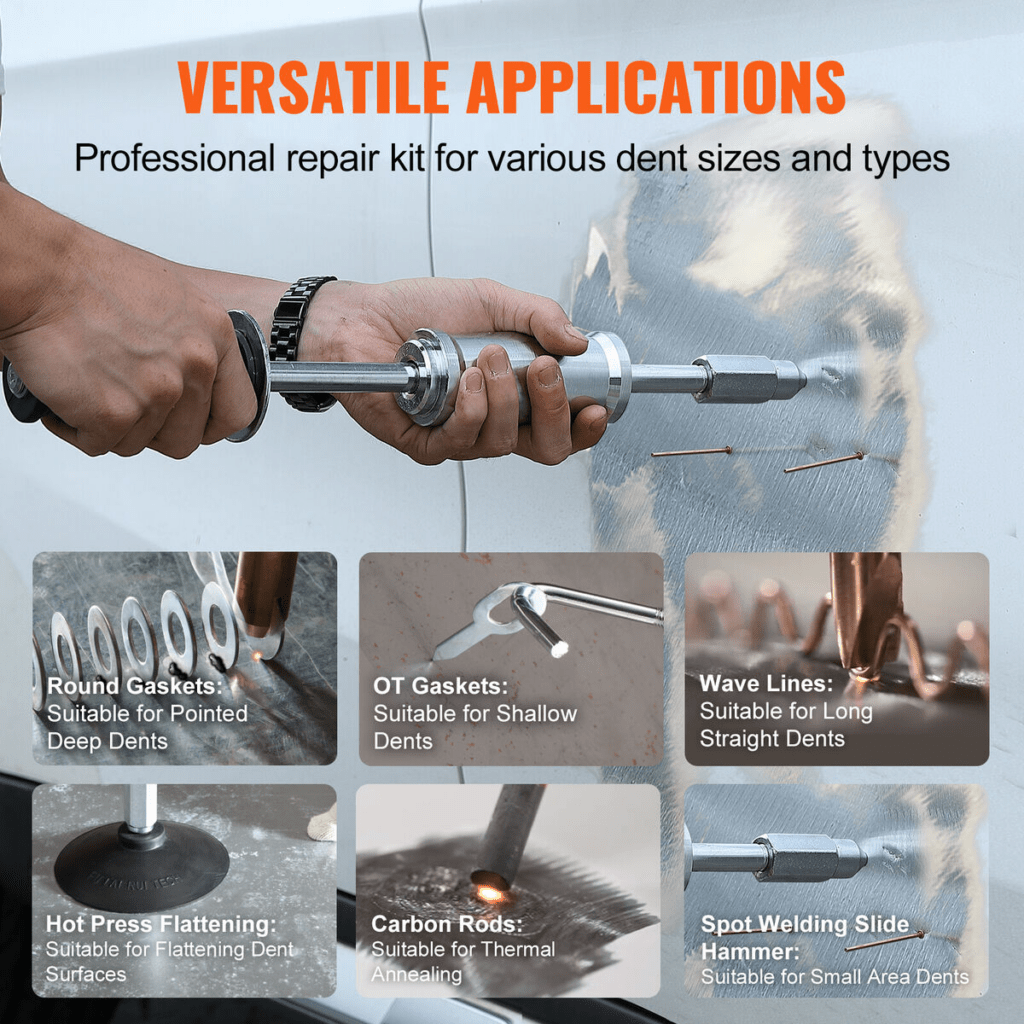
Main Applications in Bodywork:
Repairing Dents and Damage on Metal Body Panels.
The use of a stud puller is essential for various applications in automotive body repair. Here are the main applications:
Dent Repair:
Description: Dents on metal panels, often caused by minor collisions or accidental impacts, are common issues in bodywork.
Procedure: The stud puller allows welding studs onto the dented area. A traction tool, such as an inertia hammer, is then used to pull the studs and straighten the panel. This method is precise and allows the panel to regain its original shape without needing to disassemble parts.
Advantage: The repair is quick, avoiding disassembly and reassembly work, which reduces labor time and costs.
Repair of Door and Fenders Panels:
Description: Car doors and fenders are often damaged by door dings, scratches, and various impacts.
Procedure: After welding studs onto the damaged areas, the traction tool is used to straighten the panel. This method allows reaching difficult areas and precisely straightening the panel.
Advantage: Allows repairing damage without having to disassemble the doors or fenders, preserving the integrity of the panels.
Hood and Trunk Repair:
Description: Hoods and trunks can be damaged by front or rear collisions, causing significant deformations.
Procedure: By using welded studs on the deformed areas, technicians can pull the panel outward and straighten the affected surfaces. The stud puller allows precise application of traction, avoiding further damage to surrounding structures.
Advantage: Allows restoring the original shape of hoods and trunks without having to replace these costly parts.
Car Roof Repair:
Description: Car roofs can be damaged by direct impacts or accidents.
Procedure: After welding studs onto the damaged area, an extractor is used to apply controlled force and straighten the panel. This method is particularly useful for large, hard-to-reach surfaces.
Advantage: Avoids the costly replacement of the roof and allows for quick and efficient repair.
Structural Reinforcement:
Description: In addition to straightening dents, the stud puller can be used to reinforce weakened structures by welding additional anchor points.
Procedure: Studs are welded at critical points to reinforce the structure. These points can then be used to apply traction or compression forces to straighten and stabilize the structure.
Advantage: Improves the rigidity and durability of repaired structures, ensuring better safety and performance of the vehicle.
The stud puller is therefore essential and versatile for bodywork repairs. It allows treating a variety of damages with precision, speed, and efficiency, thereby reducing costs and repair time while ensuring high-quality results.
Typical metal panel straightening process with Stud welder.
Welding and Traction Process
Preparation: The surface is cleaned to ensure good adhesion of the studs.
Welding: The stud is positioned on the panel using the welding gun electrode. An intense electric current is applied to weld the stud.
Traction: The traction tool is attached to the welded stud. By pulling on the tool, the panel is straightened back to its original shape.
Removal and Finishing: The studs are removed once the panel is straightened. The surface is sanded for a smooth finish.
By coordinating these components, the stud puller allows for quick, precise, and high-quality repairs, essential for maintaining the integrity and aesthetics of vehicles.
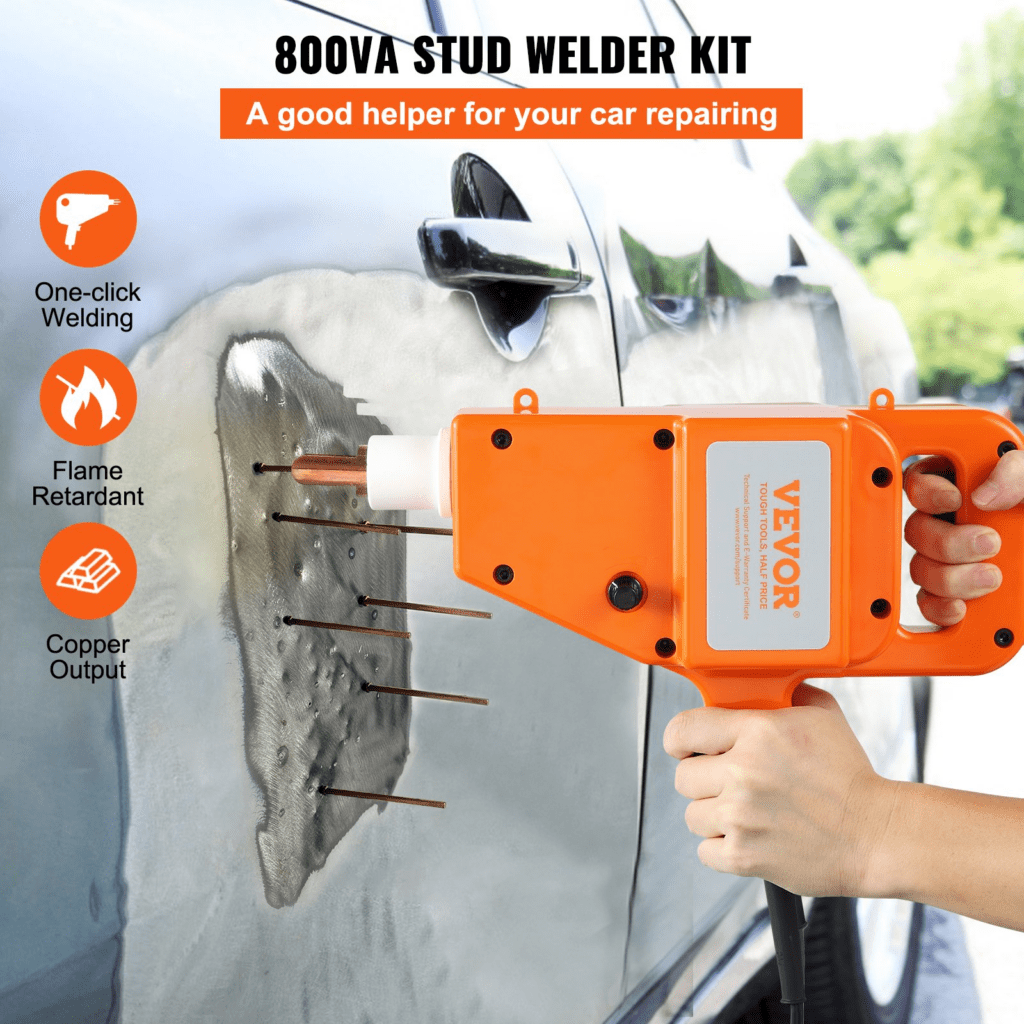
Other Possible Applications of the Stud welder.
In addition to its common use in automotive bodywork, the stud puller offers versatility that makes it useful in several other industrial fields. Here are some of the possible applications:
Industrial Sheet Metal Fabrication:
Description: The stud puller is used to weld fastening elements onto sheet metal parts in various manufacturing sectors.
Examples: Attachment of supports, conduits, and other components on metal panels used in the construction of machinery, metal structures, and industrial equipment.
Home Appliance Industry:
Description: Home appliances, often made of metal panels, require precise welding to attach components without compromising material integrity.
Examples: Attachment of hinges, motor mounts, and structural elements on refrigerators, washing machines, and ovens.
Aerospace:
Description: In the aerospace industry, the lightweight and strength of materials are crucial. The stud puller is used to attach elements to aluminum structures and other lightweight alloys.
Examples: Attachment of covering panels, internal equipment mounts, and structural reinforcement elements on aircraft.
Marine:
Description: Marine structures benefit from the stud puller’s ability to perform strong and durable welds, essential for corrosive environments.
Examples: Repair and reinforcement of boat hulls, attachment of internal components, and installation of cable supports.
Agricultural Equipment:
Description: Agricultural machines, often subjected to harsh working conditions, require robust welds to ensure their longevity and functionality.
Examples: Repair of tractor chassis, attachment of mounts for agricultural tools and equipment.
Railway Industry:
Description: Trains and other railway equipment require regular repairs and maintenance of metal structures.
Examples: Repair of wagon bodies, attachment of supports and structural elements on cars and locomotives.
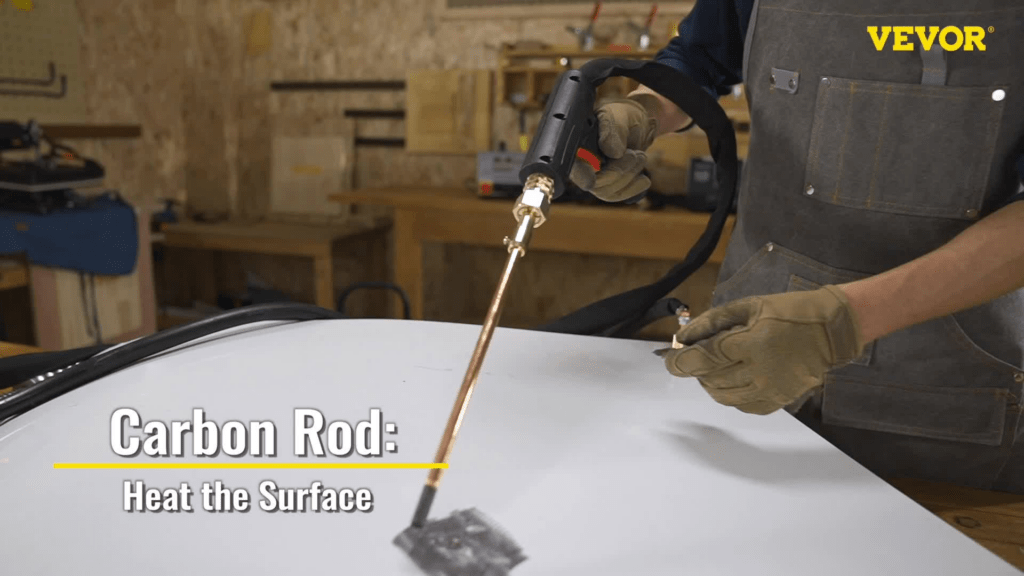
Versatility and Adaptability
The stud puller is thus extremely versatile and can be adapted to a wide range of materials and thicknesses. It is capable of welding on various metals such as steel, aluminum, and even certain specific alloys, making it useful in various sectors:
Diverse Materials: Stainless steel, aluminum, copper, and special alloys.
Variable Thicknesses: From thin metals used in home appliances to thick plates used in shipbuilding and railway construction.
The stud puller is an indispensable tool not only for automotive bodywork but also for many other industries requiring solid fixings and precise repairs on various metal structures.
Advantages of the Stud welder and Repair Quality:
The stud welder, or stud puller, is a widely used spot welding tool in the automotive industry for repairing dents and deformations of metal panels. It offers numerous advantages in terms of repair precision and quality, speed and efficiency, reduction in labor and material costs, as well as improving workshop safety. Here is a detailed overview of these advantages.
Precision and Repair Quality
Precision is a crucial criterion in any bodywork repair operation. The stud puller excels in this area by offering a precise method for straightening metal panels.
The stud welder’s ability to weld studs precisely and apply controlled traction ensures high-quality repairs. This precision translates into aesthetic and durable finishes, which is essential for maintaining the value of repaired vehicles.
Precise Welding:
Description: The stud weler uses an electrode to weld studs or pins directly onto the damaged surface of the metal panel. This welding is localized and precise, allowing technicians to target exactly the areas needing traction.
Advantage: By avoiding heat dissipation and impact on non-damaged areas, the stud puller maintains the structural integrity of the surrounding metal.
Traction Control:
Description: Once the studs are welded, a traction tool like an inertia hammer is used to pull on the studs and straighten the panel. This process allows for controlled application of force, straightening dents without creating new deformations.
Advantage: The ability to control the traction force ensures precise and effective repair, minimizing the risk of over-correcting.
High-Quality Finishing:
Description: After straightening, the studs are removed, and the surface is sanded for a smooth finish. This process ensures that the metal panel regains its original appearance without imperfections.
Advantage: Repairs made with a stud puller are durable and aesthetically pleasing, contributing to the vehicle’s residual value.
Speed and Efficiency
Speed and efficiency are essential criteria in bodywork shops, where time often equates to costs.
The speed of the welding process and the simplicity of straightening dents help reduce the overall repair time. This efficiency translates into increased workshop throughput and productivity, allowing for the processing of more vehicles in less time.
Fast Welding Process:
Description: The stud puller performs instant welding in a fraction of a second. This allows for welding multiple studs in a very short time.
Advantage: This welding speed reduces the overall repair time, enabling technicians to handle more vehicles in less time.
Effective Straightening:
Description: Once the studs are welded, dent straightening is rapid thanks to the traction tool. The pulling process is direct and efficient, requiring no disassembly of body parts.
Advantage: The efficiency of dent straightening significantly reduces repair time, thus increasing workshop throughput.
Reduction of Work Steps:
Description: Unlike traditional methods that may require disassembling panels for internal access, the stud puller allows for direct external repairs.
Advantage: Fewer work steps mean less time spent on each vehicle, increasing workshop productivity.
Reduction of Labor and Material Costs
Cost is a major concern in any bodywork repair operation. The stud puller offers significant advantages in terms of cost reduction.
By decreasing labor time and reducing the need to replace metal parts, the stud puller provides significant savings. Less materials and work time translate to lower repair costs, which is beneficial for both customers and workshops.
Less Labor:
Description: The speed and efficiency of the stud puller reduce the number of labor hours needed for each repair.
Advantage: Less labor time means reduced personnel costs, which is particularly advantageous for high-volume workshops.
Material Savings:
Description: By allowing direct repairs on damaged metal panels, the stud puller eliminates the need to replace entire parts.
Advantage: Reduced need for new parts decreases material costs, which is beneficial for the overall repair budget.
Less Waste:
Description: By repairing rather than replacing, the stud puller helps reduce metal waste.
Advantage: Reducing waste is not only economical but also environmentally friendly, which is an additional asset for workshops concerned about their environmental impact.
Improving Workshop Safety
Safety is a priority in any work environment, and the use of the stud puller contributes to creating a safer workshop.
The secure design of modern stud pullers and their ability to reduce risks of burns, electrocution, and inhalation of fumes create a safer work environment. Reducing risks associated with handling heavy parts also helps decrease injuries, thereby improving overall technician safety.
Reduced Burn Risks:
Description: The spot welding process is controlled and fast, minimizing exposure time to high temperatures.
Advantage: Less exposure time reduces the risk of burns for technicians.
Reduced Electrocution Risks:
Description: Modern stud pullers are designed with safety devices to protect against electrical risks.
Advantage: These safety devices ensure safe use of the equipment, even for less experienced technicians.
Reduced Fume Inhalation:
Description: The spot welding process generates fewer fumes and polluting gases compared to traditional welding methods.
Advantage: A work environment with fewer fumes improves air quality and reduces health risks for workers.
Safer Work Environment:
Description: By reducing the need for disassembly and reassembly, the stud puller minimizes risks associated with handling and moving heavy parts.
Advantage: Less handling of bulky parts reduces the risk of physical injuries, thereby creating a safer work environment.
The stud puller thus represents a significant advancement in the field of automotive body repair. Its advantages in terms of precision and repair quality, speed and efficiency, reduction of labor and material costs, and improvement of workshop safety make it an indispensable tool for any modern body shop.
By integrating the stud puller into repair operations, body shops can not only improve the quality and efficiency of their repairs but also create a safer and more economical work environment. It is a wise investment that offers long-term benefits for both bodywork professionals and their customers.
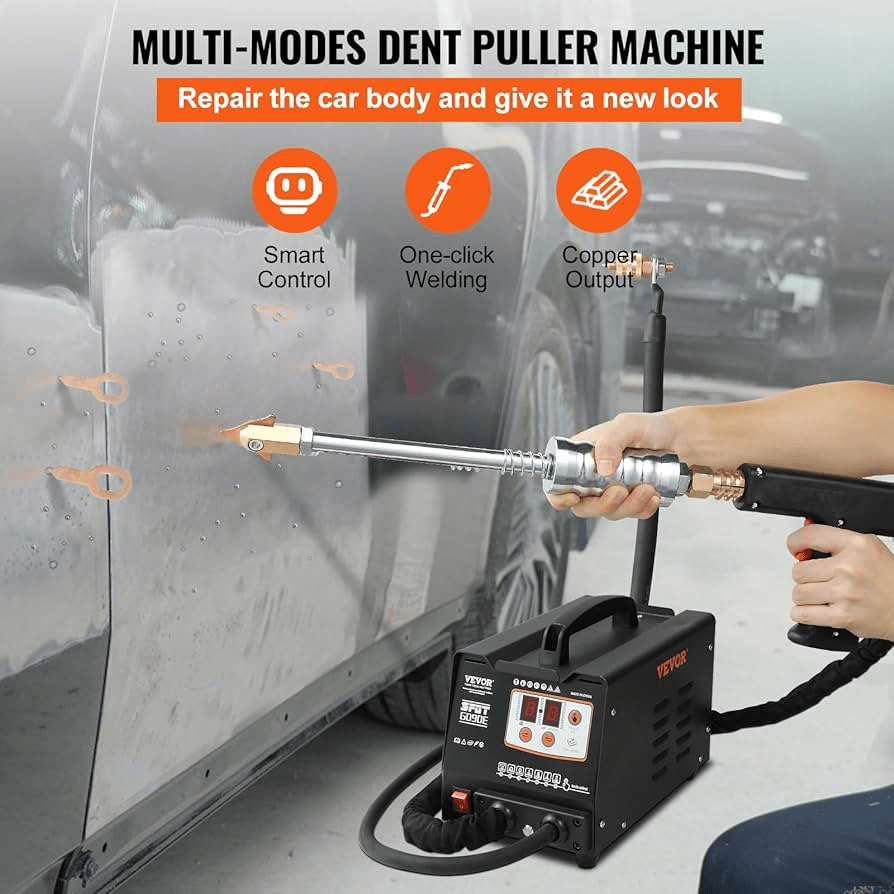
Choosing the Right Stud Puller:
Factors to Consider: Budget, Intended Applications, Technical Features.
When purchasing a stud puller, it is essential to consider several factors to ensure that the equipment will meet the specific needs of your bodywork shop. Here are the main criteria to consider: budget, intended applications, and technical features.
Budget
Initial Cost:
The cost of a stud puller can vary significantly depending on the brand, model, and included features. Establish a realistic budget by considering your workshop’s immediate needs and initial investment costs. High-end models often offer advanced features that may justify a higher cost.
Long-Term Cost:
In addition to the initial cost, consider maintenance costs, consumables (studs and accessories), and training costs. A more expensive but higher quality model can reduce long-term maintenance costs and offer increased durability, which is a wise investment.
Intended Applications
Type of Repairs:
Identify the types of repairs you perform most often, such as dent straightening, door panel repairs, or structural reinforcement. Choose a stud puller capable of handling these specific applications. For example, if you primarily work on light dents, a simpler model may suffice. For heavier work, a more powerful and versatile model is needed.
Variety of Materials:
Different metal materials require different settings. Some stud pullers are designed for specific metals like aluminum or stainless steel. Ensure that the stud puller you choose is compatible with the materials you most often repair.
Frequency of Use:
The frequency with which you use the stud puller will influence your choice. For intensive use, a robust and durable model is essential. Opt for a model designed for heavy use if your workshop handles a large volume of repairs daily.
Technical Features
Power and Capacity:
The power of the stud puller determines its capacity to weld studs on different metal thicknesses. Choose a model with power suited to your needs. A model with variable power can offer increased flexibility for different types of repairs.
Controls and Settings:
The ability to adjust power, duration, and pressure is crucial for performing precise repairs. Ensure that the stud puller offers easy-to-use settings to adapt welding to different repair situations.
Ease of Use:
An easy-to-use stud puller increases efficiency and reduces the necessary training time. Look for models with intuitive user interfaces and ergonomic features.
Portability:
Portability can be an important factor, especially if you need to move the equipment between different workstations or sites. Portable models offer additional flexibility, while stationary models may offer more power and durability.
Durability and Reliability:
A robust build and high-quality materials ensure a long lifespan of the equipment. Check user reviews and recommendations to assess the reliability of the model you are considering.
Safety:
Safety features, such as over-voltage protection and thermal safety, are essential to prevent accidents. Ensure that the model you choose complies with safety standards and includes robust safety features.
Value for Money:
A good value for money means that the cost of the equipment is justified by its performance and features. It’s not just about choosing the cheapest option, but the one that offers the best return on investment.
Examples: The Motor Guard JO1050 offers excellent value for money for small bodywork workshops.
Choosing a stud puller based on reputation and performance, it is therefore crucial to carefully evaluate the reliability, durability, technical support, and user reviews criteria. At the same time, the equipment’s performance should be examined in terms of power, precision, ease of use, versatility, safety, and value for money.
By taking these criteria into account, you can select a stud puller that not only meets your current needs but also adapts to the future requirements of your bodywork shop, thereby ensuring high-quality welds and optimal operational efficiency.
Tips for Using a Stud Puller
Best Practices for Efficient and Safe Use of a Stud Puller.
Efficient and safe use of a stud puller is essential to ensure high-quality repairs while minimizing risks to the operator. Here are some best practices to follow:
1. Preparation and Safety
Personal Protective Equipment (PPE):
Safety Goggles: To protect eyes from sparks and debris.
Heat-Resistant Gloves: To protect hands from burns.
Protective Clothing: Wear flame-resistant clothing to prevent burns.
Preparation of the Work Area:
Clean and Clear Surface: Ensure that the work area is clean and free of flammable materials.
Adequate Ventilation: Good ventilation is required to prevent the accumulation of smoke and potentially harmful gases.
Inspection of Equipment:
Check Connections: Ensure that all electrical connections are tight and in good condition.
Cable Condition: Inspect cables for wear or damage.
Traction Tool and Electrodes: Ensure that the electrodes and traction tool are clean and functional.
2. Parameters and Settings
Selecting the Right Power:
Material Type: Adjust power based on the thickness and type of material. Too high power can burn the metal, while too low power can cause a weak weld.
Pre-Tests: Conduct tests on scrap pieces to find the right settings before working on the final piece.
Adjusting Welding Duration:
Optimal Welding Time: Adjust the welding duration to ensure adequate fusion without overheating the metal.
Welding Pressure:
Uniform Pressure: Apply even pressure to avoid uneven or weak welds.
3. Welding Technique
Precise Positioning:
Placement of Studs: Place studs or pins exactly where the repair is needed to avoid unnecessary welds.
Use of Templates: Use templates or markings for precise and uniform placement of studs.
Stable Hold:
Tool Stability: Keep the welding tool stable and perpendicular to the surface to ensure an even weld.
Visual Control:
Inspection of Welds: Visually inspect each weld to ensure it is solid and properly done. Redo any welds that appear weak or defective.
4. After Welding
Cleaning:
Cleaning the Surface: Remove welding residues and clean the surface to verify the integrity of the weld.
Tool Maintenance:
Clean the welding tool and electrodes to prevent the buildup of welding residues and extend the equipment’s lifespan.
Safety Check:
Turning off the Device: Ensure that the device is turned off and disconnected from the power supply after use.
Safe Storage: Store the stud puller in a dry and safe place to prevent damage or accidents.
Dust Protection:
Measures: Use protective covers to prevent dust and dirt from accumulating on the equipment.
5. Proper Use of Equipment
Adhering to Tool Capacities:
Practices: Use the stud puller according to the manufacturer’s specifications. Do not exceed the recommended power and duration settings to avoid overheating and equipment damage.
User Manual:
Always read and follow the manufacturer’s instructions in the user manual.
Operator Training:
Ensure that all operators receive adequate training on the safe and effective use of the stud puller.
6. Electrical Safety Measures
Avoiding Moisture:
Never use the stud puller in damp or wet environments to reduce the risk of electric shock.
Disconnecting the Power Supply:
Disconnect the equipment from the power supply when not in use and before performing any maintenance.
Use of Properly Insulated Outlets and Cables:
Ensure that the outlets and cables used are properly insulated and in good condition.
7. Emergency Procedures
Fire Extinguishers Nearby:
Have appropriate fire extinguishers on hand to quickly put out any fires that may start.
First Aid Training:
Train operators in first aid to respond quickly in case of an accident.
Evacuation Plan:
Implement and communicate an evacuation plan for emergencies.
By following these safety measures, you can minimize accident risks and ensure safe and efficient use of your stud puller. Safety should always be the top priority to protect not only the equipment but also the health and safety of the operators. Constant vigilance, proper training, and attention to detail are essential to maintaining a safe and productive work environment.
Glossary
Spot Welding: A welding process used to join two metal parts at a specific point by heating them and then pressing them together.
Spot Welder (or Spot Welding Machine): A device used for spot welding, consisting of a pair of electrodes between which an electric current is applied to generate heat.
Welding Stud (or Electrode): A small metal rod used during spot welding to transfer electric current and generate necessary heat at the contact point with the pieces to be joined.
Welding Clamp: The entire system of electrodes and clamping mechanism that holds the pieces to be spot welded together during the spot welding process.
Weld Seam: The area of melted metal formed during spot welding that joins the pieces to be welded together.
Stud Puller: A tool used to remove welding studs after the spot welding process, allowing for the completion of body repair.
Structural Reinforcement: Metal parts added to an automotive body to strengthen its structure and improve its crash resistance.
Steel Sheet: A sheet material made of steel used for manufacturing automotive bodies and other metal parts.
Material Thickness: The measurement of a metal part’s thickness, which can influence spot welding parameters such as power and duration.
Dent Repair: The process of correcting minor surface damage on an automotive body by using a stud puller to pull and straighten dents.
Corrosion-Resistant Coating: A protective layer applied to metal surfaces to prevent corrosion and extend the life of the bodywork.
Parts Assembly: The act of joining multiple metal parts into a larger structure, often using spot welding.