A “Battery welder” or battery spot welder is battery manufacturing equipment. It is designed to assemble batteries from lithium cells. Conductive strips are welded between the cells to form a parallel or series network.
This tool is essential for performing precise spot welds to assemble batteries from lithium cells.
The term “Battery welder” in American English translates to “soudeuse par points pour batterie” in French.
SPOT WELDING / STUD WELDER
SOUDURE PAR POINT / TIRE CLOU
PUNKTSCHWEIBER / DENT PULLER
SOLDADOR POR PUNTOS / SOLDADOR DE PERNOS
SALDATURA A PUNTI / SALDATORE DI TASSELLI
Trusted and verified affiliates links
Introduction to the Battery welder
Definition and Operation
Definition:
A Battery welder (Battery Spot Welder) is a specialized device. It is used to weld battery cells using the spot welding process. This tool is essential for assembling battery packs in a secure and reliable manner. It ensures strong and durable electrical connections between the cells.
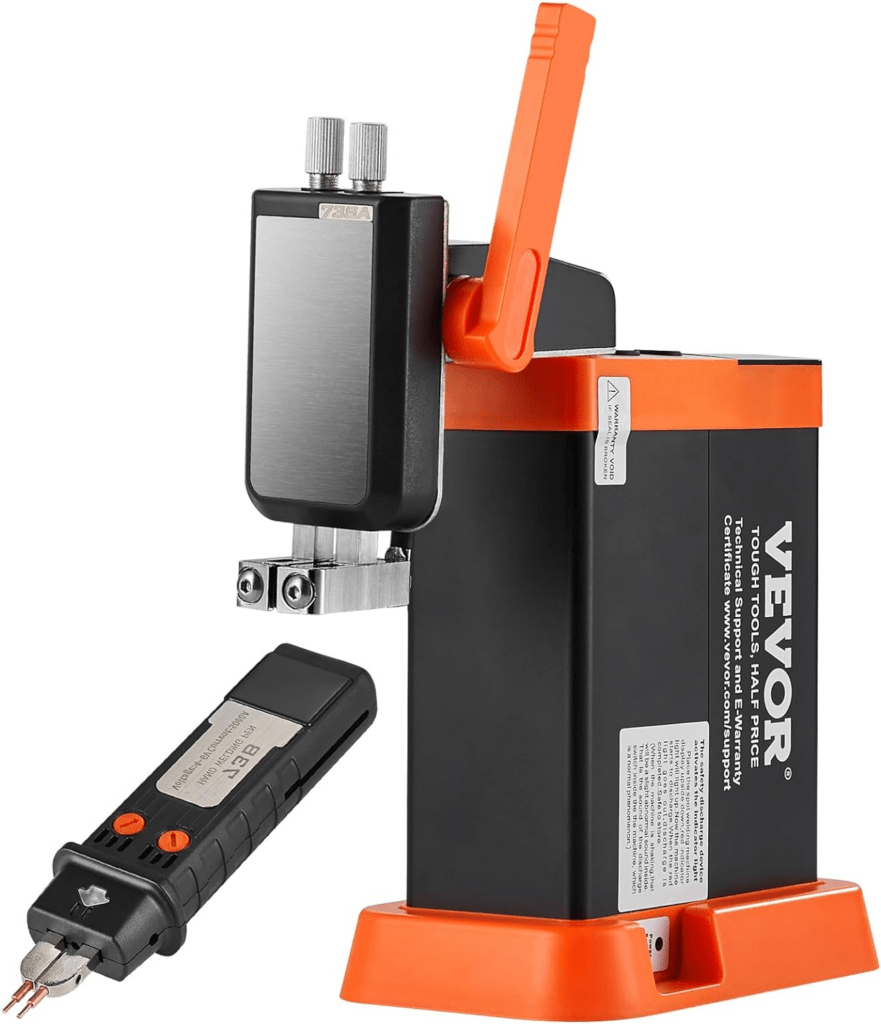
Battery spot welding involves applying an electrical pulse through electrodes to locally heat the metal strips (often nickel) and the cell terminals, thereby fusing them together. The Battery welder is designed to provide precise power and welding duration settings, allowing it to adapt to different material thicknesses and battery cell specifications.
Main Components of a Battery welder:
- Welding Electrodes: Transfer electrical current to perform the weld.
- Power Controller: Adjusts the amount of energy delivered during welding.
- Cell Holders: Maintain the position of the cells during the welding process.
- Safety Mechanisms: Such as sensors and protections to prevent overloading and accidents.
Operation:
A Battery welder or battery spot welder operates using the spot welding process to assemble battery cells securely and efficiently. Here is a detailed explanation of its operation:
Preparation of Cells and Strips:
Cell Inspection: Each battery cell is checked with a multimeter to ensure it has the same voltage as the others, preventing imbalances.
Cell Arrangement: The cells are placed in a holder that keeps them in position during the welding process. They can be arranged in series, parallel, or a combined configuration according to the battery specifications.
Nickel Strip Preparation: The metal strips, usually nickel, are cut to the appropriate size to connect the cell terminals. They are cleaned to ensure good electrical conductivity.
Setting up the Battery welder:
Power Adjustment: The welder’s power level is adjusted based on the thickness of the strips and the cell terminals. Adequate power is essential to avoid overheating or damaging the cells.
Welding Duration Adjustment: The duration of the welding pulse is set to control the time the current is applied. This ensures optimal fusion of the materials.
Battery welder process:
Electrode Positioning: The welder’s electrodes are aligned on the nickel strip and the cell terminals. The strip must contact the terminals precisely.
Applying the Welding Pulse: An electrical pulse is sent through the electrodes, generating intense heat at the contact point. This heat locally melts the strip and the cell terminals, fusing them together.
Weld Verification: After each weld, the operator visually and mechanically checks the connection’s solidity. They ensure there are no weak weld points or excessive burns.
Finalization and Testing:
Final Assembly: The strips are welded according to the desired connection scheme (series or parallel). The final connections are insulated to prevent short circuits.
Battery Testing: A multimeter is used to check the overall voltage of the assembled battery pack. Charge and discharge tests may be performed to ensure the battery functions correctly.
Safety and Maintenance:
Personal Protective Equipment: Operators must wear personal protective equipment (heat-resistant gloves, safety glasses) to prevent injuries from sparks and heat.
Maintenance: The Battery welder must be regularly maintained, including cleaning the electrodes and checking electrical connections to ensure optimal performance and prolong the device’s lifespan.
Main applications of the Battery welder:
Battery welders, or battery spot welders, are essential tools for various industries where assembling battery packs is crucial.
Here are the main applications of these devices:
Assembly of lithium-ion (Li-ion) battery packs:
Used in portable electronic devices such as smartphones, tablets, and laptops.
Also employed in portable power tools like drills, saws, and other wireless tools.
Nickel-Metal Hydride (NiMH) Batteries: Used in household appliances like cordless vacuum cleaners, electric toothbrushes, and razors.
Also used in certain industrial applications requiring rechargeable batteries.
Lithium-Polymer (Li-Po) Batteries: Frequently used in drones, model airplanes, and remote-controlled vehicles due to their lightweight and high capacity.
Electric and hybrid vehicles:
Electric Cars (EV): Battery welders are used to assemble the battery modules that power electric vehicles, providing a reliable and durable energy source.
Hybrid Vehicles (HEV): Assembling battery packs used to provide electrical assistance to internal combustion engines, thereby improving overall energy efficiency.
Electric Bikes and Scooters: Creating compact and powerful battery packs to power personal electric vehicles.
Renewable energy and energy storage systems:
Manufacturing batteries for domestic and industrial energy storage systems allows energy produced by solar panels and wind turbines to be stored.
They are commonly used in microgrids to stabilize energy supply and enhance the resilience of electrical networks.
Medical equipment:
Portable Medical Devices: Used in portable medical equipment such as heart monitors, insulin pumps, and other devices requiring a reliable power source.
Medical Carts: Assembling batteries for medical carts used in hospitals, ensuring continuous power for critical medical equipment.
Household appliances and consumer products:
Wireless Tools: Manufacturing battery packs for a variety of wireless tools used in domestic and professional applications.
Household Appliances: Assembling batteries for portable household devices, such as cordless vacuum cleaners, electric toothbrushes, and lawn mowers.
Industrial applications
Robots and Automation Systems: Creating battery packs for industrial robots and automated systems, providing a reliable energy source for continuous operations.
Uninterruptible Power Supplies (UPS): Manufacturing batteries for UPS systems, ensuring backup power in case of power outages for critical equipment.
Advantages of the Battery welder:
Using a Battery welder offers numerous advantages over other welding processes for battery assembly. Here are the main benefits:
1. Precision and quality of Battery welder
Precise Power Control:
Battery welders allow very precise control of power and welding pulse duration. This ensures consistent and high-quality welds, essential for the reliability of battery packs.
Clean Welds:
Spot welding creates clean welds with minimal spatter, reducing the need for post-weld cleaning.
2. Speed and efficiency
Fast Process:
Spot welding is a fast process, capable of making welds in a few milliseconds, significantly speeding up production time.
Easy Automation:
Battery welders can be easily integrated into automated systems, increasing productivity and reducing labor costs.
3. Reduction of labor and material costs
Less Material Needed:
Compared to other methods, spot welding uses less filler material, thereby reducing production costs.
Waste Reduction:
By minimizing spatter and welding waste, Battery welders contribute to more efficient material usage.
4. Safety and improved working conditions
Less Fumes and Gases:
Spot welding generates fewer fumes and harmful gases compared to other welding processes, improving air quality in the workshop and reducing health risks for operators.
Reduced Risk of Burns and Electrocution:
Battery welders are designed to be safe to use, with built-in protection systems to prevent accidents related to burns and electrocution.
5. Durability and reliability of welds
Strong Connections:
Spot welds are robust, ensuring strong connections. They resist vibrations and shocks, making them suitable for mobile and industrial applications.
Low Risk of Cell Overheating:
By precisely controlling the applied energy, Battery welders minimize the risk of overheating battery cells, thus preserving their integrity and long-term performance.
6. Flexibility and adaptability
Wide Range of Materials and Thicknesses:
Battery welders can weld a variety of materials and thicknesses, including nickel, copper, and aluminum strips, offering great flexibility for different applications.
Compatibility with Various Battery Types:
Whether dealing with lithium-ion, nickel-metal hydride, or other types of rechargeable cells, Battery welders are suitable for a multitude of battery configurations.
Battery welders stand out for their precision, speed, safety, and efficiency, making them the tool of choice for assembling battery packs. Their ability to create clean and strong welds, reduce material and labor costs, and offer flexibility in applications makes them indispensable in many industries, ranging from consumer electronics to electric vehicles and energy storage systems.
Choosing the right Battery welder:
Factors to consider: Budget, intended applications, technical features.
When purchasing a Battery welder, it is essential to consider several factors to ensure the equipment meets specific needs. Here are the main criteria to consider: budget, intended applications, and technical features.
Budget
Initial Cost:
The cost of a Battery welder can vary significantly based on the brand, model, and included features. Establish a realistic budget considering your workshop’s immediate needs and initial investment costs. High-end models often offer advanced features that may justify a higher cost.
Long-term Cost:
In addition to the initial cost, consider maintenance, consumables, and training costs. A more expensive but higher-quality model can reduce long-term maintenance costs and offer increased durability, making it a wise investment.
Technical features
Power and capacity:
The power of the Battery welder determines its ability to weld cells of different metal thicknesses. Choose a model with power suitable for your needs. A model with variable power can offer increased flexibility for different types of assemblies.
Controls and settings:
The ability to adjust power, duration, and pressure is crucial for performing precise assemblies. Ensure that the Battery welder offers easy-to-use settings to adapt welding to different situations.
Ease of use:
An easy-to-use Battery welder increases efficiency and reduces the training time required. Look for models with intuitive user interfaces and ergonomic features.
Portability:
Portability can be an important factor, especially if you need to move the equipment between different workstations or sites. Portable models offer additional flexibility, although stationary models may provide more power and durability.
Durability and reliability:
Robust construction and high-quality materials ensure a long lifespan of the equipment. Check user reviews and recommendations to assess the reliability of the model you are considering.
Safety:
Safety features, such as surge protection devices and thermal protections, are essential to prevent accidents. Ensure that the model you choose complies with safety standards and includes robust safety features.
Accessories and consumables:
Available accessories, such as different types of strips and welding electrodes, can enhance the efficiency and versatility of your Battery welder. Opt for a model compatible with a wide range of easily available accessories and consumables.
Technical choices
Choosing a Battery welder suitable for your needs involves a careful evaluation of several key factors: budget, intended applications, and technical features. By taking the time to consider each aspect, you can ensure that the equipment you choose not only meets your current requirements but also adapts to your workshop’s future needs.
Investing in a quality Battery welder can transform the efficiency and precision of your assemblies while reducing long-term costs and improving the safety of your workshop. Whether you are a high-volume manufacturing workshop or an independent technician, choosing the right Battery welder is a strategic decision that will impact your overall business performance.
Comparison of different types of Battery welders available on the market (Portable, stationary, etc.).
The choice of a Battery welder depends on several factors such as the intended application, frequency of use, budget, and required technical features. Battery welders are primarily classified into three categories: portable, stationary, and robotic. Here is a comprehensive comparison of these types of Battery welders.
1. Portable Battery welder
Description: Portable Battery welders are compact and lightweight. They are easily transportable. They are suitable for mobile repairs or workshops with limited space.
Features:
Portability: Easy to carry, perfect for on-site repairs.
Power: Generally less powerful than stationary models but sufficient for most thin to medium sheet repairs.
Usage: Simple to use with a quick learning curve.
Applications: Dent repairs, light panel fixing, use in confined spaces.
Advantages:
Mobility: Ideal for technicians working at different sites.
Cost: Often less expensive than stationary and robotic models.
Installation: Requires minimal installation and setup.
Disadvantages:
Limited Power: Less suitable for heavy-duty work or thick materials.
Durability: Less robust for intensive use compared to stationary models.
2. Stationary Battery welder
Description: Stationary Battery welders are fixed machines installed in a workshop. They offer more power and advanced features, suitable for heavy-duty work and intensive use.
Features:
Power: Higher, capable of handling thicker materials.
Stability: Fixed setup allows for more stable and continuous use.
Usage: Advanced user interface with precise settings for different types of materials and nails.
Applications: Heavy repairs, serial production, structural reinforcement, fixing heavy components.
Advantages:
Performance: More powerful and suitable for a wide range of tasks.
Durability: Designed for intensive and long-term use.
Features: Advanced options like digital control, memory settings, etc.
Disadvantages:
Mobility: Not portable, fixed to one location.
Cost: More expensive than portable models.
3. Robotic Battery welder
Description: Robotic Battery welders integrate into automated systems. They are suitable for large-scale industrial applications. They are used in automated production lines.
Features:
Automation: Controlled by robots, allowing operations without human intervention.
Precision: Extremely precise with automatic settings for a wide variety of tasks.
Usage: Advanced programming for repeated and uniform welding cycles.
Applications: Serial production, industries requiring high precision and yield, such as automotive and aerospace.
Advantages:
Efficiency: High efficiency and productivity due to automation.
Quality: Uniform and high-quality welds with consistent precision.
Safety: Fewer risks for operators thanks to complete automation.
Disadvantages:
Cost: Very expensive, high initial investment and maintenance costs.
Complexity: Complex installation and programming, requiring specialized training.
Comparison of key factors
Criterion | Portable | Stationary | Robotic |
---|---|---|---|
Portability | Very high, easy to transport | Low, fixed in one place | None, integrated into fixed systems |
Power | Moderate, suitable for light to medium materials | High, suitable for a wide range of materials and tasks | Very high, suitable for heavy industrial applications |
Ease of Use | Easy, quick learning curve | Moderate, requires initial training | Complex, requires advanced programming and training |
Applications | Light repairs, mobile use | Heavy repairs, serial production, intensive use | Serial production, automated industrial applications |
Cost | Low to moderate | Moderate to high | Very high |
Durability | Moderate | High, designed for intensive use | Very high, designed for continuous production |
Advanced Features | Limited | Advanced, with digital control options | Very advanced, full integration with automated production systems |
The choice of a Battery welder will primarily depend on your specific needs, budget, and work environment. For mobile repairs and workshops with limited space, a portable Battery welder is ideal. If you need more power and durability for intensive tasks, a stationary model is more appropriate. Finally, for large-scale industrial applications requiring serial production, robotic Battery welders offer an optimal solution despite their high cost and complexity.
By carefully evaluating these criteria and understanding the advantages and disadvantages of each type of Battery welder, you can make an informed choice that will maximize the efficiency and profitability of your workshop.
Tips for using a Battery welder
Using a Battery welder (battery spot welder) requires specific precautions and methods to ensure safe and effective operations. Here are some tips to maximize performance and safety when using this type of equipment.
Preparation and safety
Personal protective equipment (PPE):
Safety Glasses: To protect your eyes from sparks and debris.
Heat-Resistant Gloves: To protect your hands from burns.
Protective Clothing: Wear fire-resistant clothing to prevent burns.
Safety Shoes: Use shoes with insulating soles to reduce the risk of electric shock.
Work area preparation:
Clean and Clear Surface: Ensure the work area is clean and free of flammable materials.
Adequate Ventilation: Good ventilation is necessary to prevent the buildup of potentially harmful fumes and gases.
Equipment inspection:
Connection Check: Ensure all electrical connections are tight and in good condition.
Cable Condition: Inspect cables for any wear or damage.
Batteries: Check the charge level and condition of the batteries. Replace any damaged or worn batteries.
Settings and adjustments
Selecting the appropriate power:
Material Type: Adjust the power based on the thickness and type of material to be welded. Too high power can burn the metal, while insufficient power can result in weak welds.
Preliminary Tests: Conduct tests on scrap pieces to correctly set the power before working on the final piece.
Adjusting the Welding Duration: Optimal welding time: Adjust the welding duration to ensure adequate fusion without overheating the metal.
Welding pressure:
Uniform Pressure: Apply uniform pressure to avoid uneven or weak welds.
Maintenance and upkeep
Ensuring regular maintenance and upkeep of your Battery welder (battery spot welder) is essential to guarantee its proper functioning, prolong its lifespan, and prevent breakdowns. Here is a detailed guide on the steps and recommended practices for maintaining this equipment.
Regular inspection
Visual inspection:
Cables and Connectors: Regularly check the condition of cables and connectors for any wear, cuts, or damage. Replace damaged cables immediately.
Device Housing: Inspect the housing to ensure there are no cracks, damages, or signs of wear.
Electrodes: Examine the electrodes to ensure they are clean and in good condition. Replace them if they are worn or damaged.
Cleaning
Cleaning components:
Electrodes: Clean the electrodes after each use to remove welding residues. Use a wire brush or a dry cloth.
Ventilation: Ensure that ventilation slots are not blocked by dust or debris. Use compressed air to clean them if necessary.
External Surfaces: Wipe the external surfaces of the device with a damp cloth. Never use harsh solvents that could damage the components.
Preventive maintenance
Connection checks:
Tightening Connections: Ensure that all electrical connections are tight to prevent loose contacts or short circuits.
Battery Condition: Regularly check the condition of the batteries. Replace batteries that show signs of failure, swelling, or leakage.
Calibration and settings:
Parameter Calibration: Ensure that the power and welding duration settings are correctly calibrated. Refer to the user manual for calibration specifications.
Software updates:
If your device is equipped with software, regularly check for updates provided by the manufacturer and install them.
Storage
Storage conditions:
Dry Environment: Store the device in a dry place to prevent corrosion of electrical components.
Controlled Temperature: Avoid storing the device in areas where the temperature is extremely high or low.
Shock Protection: Store the device in a place where it is unlikely to be bumped or damaged by other objects.
Documentation and tracking
Maintenance log:
Inspection Records: Keep a log of inspections and maintenance work performed. Note dates, observations, and actions taken.
Issue tracking:
Document any problems encountered and the solutions applied to facilitate future troubleshooting and resolution.
Manual references:
Always refer to the user manual provided by the manufacturer for specific instructions on maintenance and repairs. Follow the manufacturer’s recommendations to ensure compliance and safety.
Training and awareness
User training:
Proper Usage: Ensure that all users of the device are trained in its correct use and in performing basic maintenance tasks.
Safety awareness:
Emphasize the importance of safety practices and the use of personal protective equipment (PPE).
By following these maintenance and upkeep tips, you can ensure reliable and safe operation of your Battery welder. Regular inspections, proper cleaning, preventive checks, adequate storage, and thorough documentation contribute to prolonging the device’s lifespan and preventing costly breakdowns.
Glossary
A
Amperage: The measurement of the amount of electrical current flowing through a circuit, crucial for determining welding power.
Anode: The positive electrode in a welding circuit.
B
Battery spot welder: A device used to weld metal materials using energy stored in a battery, often used for assembling battery packs and metal sheets.
Stud: A metal rod used in the welding process to fix metal parts together.
C
Cathode: The negative electrode in a welding circuit.
Ground cable: A cable that connects the welding device to the workpiece to complete the electrical circuit.
Connector: A device used to connect welding cables to the device or workpiece.
D
Welding duration: The time during which the welding current is applied to create the weld.
E
Electrode: A conductor through which current enters or exits in the welding process.
Electrolyte: A substance that conducts electricity in batteries, often a liquid solution or gel.
Personal protective equipment (PPE): Equipment such as gloves, safety glasses, and heat-resistant clothing used to protect the operator during welding.
F
Fusion: The process of melting materials at their contact surfaces to form a solid bond upon cooling.
G
Template: A tool used to ensure precise and uniform placement of welds or studs.
I
Current intensity: The measurement of the amount of electric charge passing through the welding circuit per unit time, often measured in amperes.
M
Preventive maintenance: Regular inspection, cleaning, and checking procedures to ensure the proper functioning of welding equipment.
User manual: A guide provided by the manufacturer containing instructions for using and maintaining the welding equipment.
P
Welding parameters: Settings of the welding device, such as power and welding duration, adjusted according to the material specifications to be welded.
Welding reach: The ability of the welding device to reach and weld different parts of the workpiece.
Pulsation: A welding technique where current is applied in rapid pulses to control the amount of heat and fusion.
R
Power adjustment: The adjustment of the level of electrical current supplied by the welding device to achieve an optimal weld.
S
Electrical safety: Practices and measures to prevent electric shocks when using welding equipment.
Welding: The process of melting two metal materials to create a permanent bond.
Work surface: The area where welding is performed. It must be clean and well-prepared to ensure high-quality welds.
T
Welding technician: A trained and qualified person to perform welding operations.
V
Ventilation: The process of providing adequate airflow to remove harmful fumes and gases produced during welding.
Voltage: The electrical potential difference between two points in a circuit. It determines the force with which the electrical current is pushed through the circuit.